At present, the new Feed-Sup has been officially launched. Compared with the previous two generations of systems, Feed-Sup has made significant improvements and optimizations in the control method and feeding function, and can more effectively and accurately realize the biological fermentation process. The feeding control in the company has successfully achieved the iterative development of the product and further met the feeding requirements of different customers.
The introduction of the new entry control method can more effectively realize the replenishment accuracy of the culture medium or fermentation substrate during the fermentation process, ensure the concentration, temperature or oxygen content of nutrients in the fermenter, and support the fermentation in an ideal state.
Both the main control screen icon of the system and the main interface of feeding control can display the rotation speed of the feeding pump and the flow rate of the pumped liquid in real time, and the operation status of the feeding pump can be understood by observation.
2. The calibration of the feeding material and the switching of the feeding pipe
Enter the set amount, and pump the set amount of liquid through the manual feeding function, and then input the actual pumped liquid volume into the actual amount, and finally click the calibration button. The calibration of the feeding pump can be achieved.
Select the tube number of the silicone tube installed on the feeding pump, and then click the reset button to switch to the peristaltic pump coefficient of the target silicone tube, and then the silicone tube of 16#, 19#, and 25# can be switched to meet different requirements. Replenishment requirements.
3. The function of calculating and clearing the accumulated feeding amount
The icon on the main control screen of the system can display the accumulated feed amount during the fermentation process in real time, and the clear button can also clear the accumulated feed amount, so as to customize the recording starting point of the accumulated feed amount.
During the fermentation process, input the required correlation speed, and the conditions of feeding positive correlation pH or feeding negative correlation pH, the system can perform feeding unidirectional correlation pH.
During the fermentation process, input the required associated rotation speed, and the conditions for the positive correlation DO of the feeding or the negative correlation DO of the feeding, and the system can perform the feeding correlation DO, and perform multiple adjustments to the DO to meet the diverse needs of customers.
The above is the previous product feeding system. Feed-Sup has updated the functions of equation feeding and exponential feeding on the basis of retaining 1th and 2th. Generally, high-density fermentation is carried out under the condition of nutrient limitation. Usually, carbon source material is used as the limiting nutrient, and nutrients are supplemented through constant-speed feeding, exponential feeding and other feeding methods to achieve high-density fermentation culture.
In the case of E. coli, the exponential feeding strategy not only allowed cells to grow at a constant specific growth rate, but also suppressed the accumulation of the metabolic by-product acetate by controlling the specific growth rate at the critical specific growth rate for acetate accumulation. Reduce the side effects of acetic acid on fermentation culture.
Based on the above requirements, the Feed-Sup feeding function is set as follows:
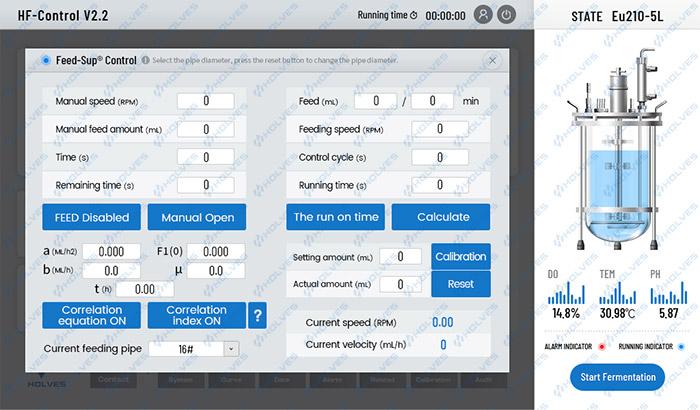
(Feed-Sup® feeding control interface)
The description of the main parameters of equation feeding and exponential feeding is as follows:
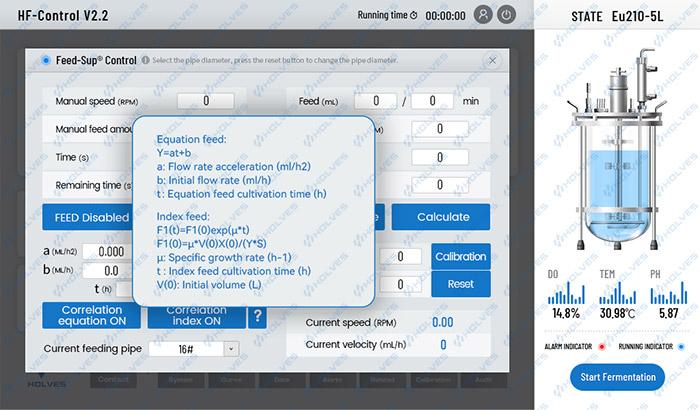
(Feed-Sup® equation feed, index feed instructions)
The development and use of equation feed and exponential feed systems have enabled HOLVES to further upgrade the feeding function of existing products, satisfying customers' precise control and operational convenience in the actual fermentation process, and maintaining scientific research results. Scientific rigor is also the development pursuit that HOLVES has always been committed to in the field of biological fermentation.
Feed-Sup® The upgrade of the feeding control method
Feed 1th adopts the analog control method, Feed 2th adopts the pulse control method, and Feed-Sup has made improvements on the basis of the former two and adopts the RS-485 communication method. For comparison, see the previous the public article "Influence of Stepper Motor Drive Mode on Peristaltic Pump Precision" .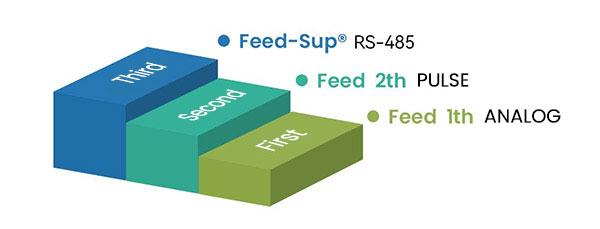
The introduction of the new entry control method can more effectively realize the replenishment accuracy of the culture medium or fermentation substrate during the fermentation process, ensure the concentration, temperature or oxygen content of nutrients in the fermenter, and support the fermentation in an ideal state.
Feed-Sup® The upgrade of the feeding function
Feed 1th and Feed 2th feeding functions are based on the display and application of manual and on-time feeding modules in the traditional feeding process to ensure the relative control of pH and DO in the feeding process.-
General functions
Both the main control screen icon of the system and the main interface of feeding control can display the rotation speed of the feeding pump and the flow rate of the pumped liquid in real time, and the operation status of the feeding pump can be understood by observation.
2. The calibration of the feeding material and the switching of the feeding pipe
Enter the set amount, and pump the set amount of liquid through the manual feeding function, and then input the actual pumped liquid volume into the actual amount, and finally click the calibration button. The calibration of the feeding pump can be achieved.
Select the tube number of the silicone tube installed on the feeding pump, and then click the reset button to switch to the peristaltic pump coefficient of the target silicone tube, and then the silicone tube of 16#, 19#, and 25# can be switched to meet different requirements. Replenishment requirements.
3. The function of calculating and clearing the accumulated feeding amount
The icon on the main control screen of the system can display the accumulated feed amount during the fermentation process in real time, and the clear button can also clear the accumulated feed amount, so as to customize the recording starting point of the accumulated feed amount.
-
Manual feed
-
Feed on time
-
Feed related pH
During the fermentation process, input the required correlation speed, and the conditions of feeding positive correlation pH or feeding negative correlation pH, the system can perform feeding unidirectional correlation pH.
-
Feed related DO
During the fermentation process, input the required associated rotation speed, and the conditions for the positive correlation DO of the feeding or the negative correlation DO of the feeding, and the system can perform the feeding correlation DO, and perform multiple adjustments to the DO to meet the diverse needs of customers.
The above is the previous product feeding system. Feed-Sup has updated the functions of equation feeding and exponential feeding on the basis of retaining 1th and 2th. Generally, high-density fermentation is carried out under the condition of nutrient limitation. Usually, carbon source material is used as the limiting nutrient, and nutrients are supplemented through constant-speed feeding, exponential feeding and other feeding methods to achieve high-density fermentation culture.
In the case of E. coli, the exponential feeding strategy not only allowed cells to grow at a constant specific growth rate, but also suppressed the accumulation of the metabolic by-product acetate by controlling the specific growth rate at the critical specific growth rate for acetate accumulation. Reduce the side effects of acetic acid on fermentation culture.
Based on the above requirements, the Feed-Sup feeding function is set as follows:
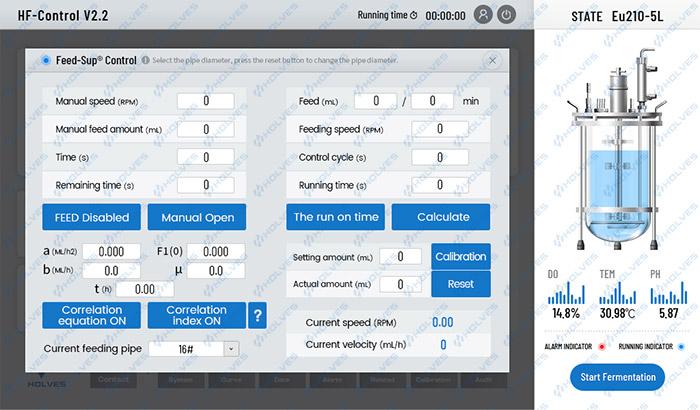
(Feed-Sup® feeding control interface)
-
Equation feed
-
Index feed
The description of the main parameters of equation feeding and exponential feeding is as follows:
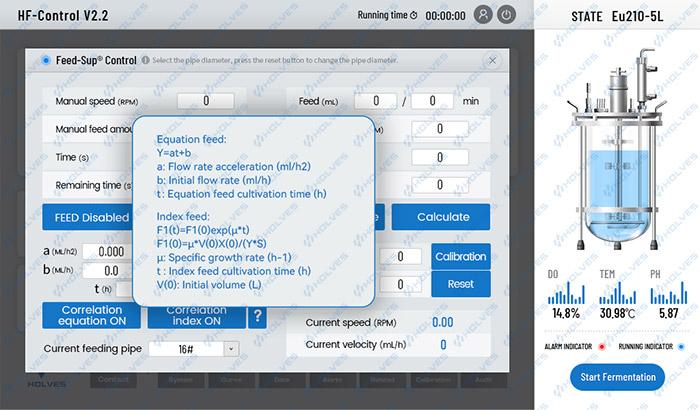
(Feed-Sup® equation feed, index feed instructions)
The development and use of equation feed and exponential feed systems have enabled HOLVES to further upgrade the feeding function of existing products, satisfying customers' precise control and operational convenience in the actual fermentation process, and maintaining scientific research results. Scientific rigor is also the development pursuit that HOLVES has always been committed to in the field of biological fermentation.