In the modern biopharmaceutical industry, antibody-drug couplings (ADCs) and monoclonal antibody drugs have become hotspots for drug development and application due to their high degree of targeting, excellent efficacy, and great potential in the treatment of many diseases. However, the production of these complex drugs cannot be achieved without the support of advanced equipment, in which bioreactors and tangential flow filtration (TFF) systems play a crucial role. In this paper, we will synthesize the application of these two types of equipment and their synergistic effects in the production of antibody drugs.
Precise environmental control
1. Temperature control
During the culture process, the right temperature (37°C) is essential to maintain normal cell metabolism and growth rate. Similarly, during the antibody production phase, small fluctuations in temperature can affect the activity of intracellular enzymes, which in turn can alter cellular metabolic pathways and the rate of antibody synthesis. For the antibody component of ADC drugs, a stable temperature helps to ensure proper post-translational modification processes such as folding and glycosylation, which have stringent temperature requirements. The right temperature improves the quality and activity of the antibody, and provides high-quality antibody raw material for subsequent coupling to the drug linker.
HOLVES bioreactors use electric heating, coil heat transfer (jacketed temperature control is also available), combined with sophisticated temperature sensors and controllers, to precisely control the temperature inside the tank to the temperature required for cell growth.
2. pH adjustment
Cells produce acidic or alkaline substances, such as lactic acid and ammonia, during growth and metabolism. Depending on the needs of the cell line, the bioreactor has to maintain the pH value of the culture medium in a range suitable for the growth of the cells (generally 7.2 - 7.4). In the coupling reaction stage of ADC drug preparation, pH value affects the binding efficiency and selectivity of the drug linker to the antibody, and an inappropriate pH value may lead to heterogeneous coupling, resulting in a poor quality ADC drug product.
Changes in the value are closely monitored by a pH monitoring system and adjusted by the addition of an acid or base solution through an automated control system. Optionally, control can be performed using CO₂ and acid or base solution addition.
3.DO (Dissolved Oxygen) Concentration Management
Adequate oxygen supply is essential for cell growth and antibody production. The bioreactor automatically controls the DO concentration in the fermenter by adjusting parameters such as aeration, stirring speed and oxygen concentration to meet the oxygen demand of the cells. The appropriate level of dissolved oxygen can affect the metabolic state of the cells, which in turn affects the glycosylation level of the antibodies and has an important impact on the activity, stability and in vivo pharmacokinetic properties of the ADC drug.
4. Cell growth process to monitor
Viable Cell Density: During the whole cultivation process, a small amount of samples need to be taken out of the bioreactor periodically to monitor the growth status of the cells, and to judge whether to adjust the cultivation conditions according to the growth situation, in order to ensure that the cells are in the optimal state of growth and production. You can also choose to assemble a real-time detection of live cell density sensor to save labor and time as well as improve productivity.
Anti-foaming system: During the cell culture process, foam may be generated due to operations such as aeration and agitation. HOLVES fermenters are equipped with defoaming devices such as mechanical defoaming paddles or automatic addition of defoamer.
The configuration of sensors for ORP, online OD, and tail gas analysis (including OUR, CER, RQ, etc.) allows the cell growth status to be monitored at all times.
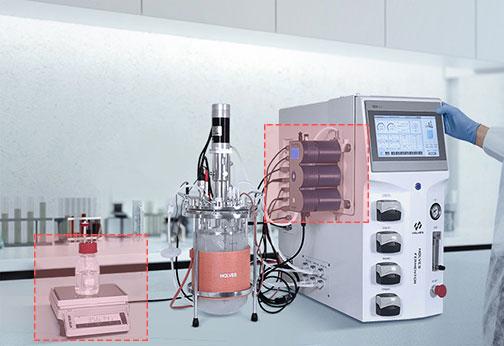
1. Concentration and desalting of antibodies
In the production of antibody drugs, the concentration of antibodies is often low, and they need to be concentrated to increase their concentration to meet the needs of subsequent processes and quality control. The tangential flow filtration system can effectively retain antibody macromolecules by selecting membranes with appropriate pore sizes, allowing small molecule impurities and water to pass through the membrane, thus realizing the concentration of antibodies. Meanwhile, during the concentration process, the salts and buffer components in the antibody solution can also be removed to achieve the effect of desalination, providing pure antibody raw materials for the subsequent coupling reaction or other process steps.
2. Purification of products
For ADC production, after coupling reaction, tangential flow filtration system can further play its purification role. By selecting filter membranes with different pore sizes, TFF technology can remove unreacted antibodies and small molecules of drugs and realize the separation of ADC from free toxins or antibodies. This process is important for improving the purity and quality of ADC products, ensuring the structural integrity and pharmacodynamic properties of the final drug product.
3. Buffer exchange
Tangential Flow Filtration systems can also be used to replace the buffer in a drug formulation. Through TFF technology, the original buffer in the drug solution is exchanged for a liquid that is more conducive to achieving storage stability, thus ensuring the stability and activity of the drug.
Meanwhile, the tangential flow filtration system is not only capable of efficiently concentrating and purifying the antibody during the downstream processing to improve the purity and quality of the antibody, but also capable of replacing the buffer to optimize the stability and activity of the drug preparation. This process lays a solid foundation for the final molding of the antibody drug, ensuring the performance and safety of the drug product.
Through the synergistic effect of the two, from cell culture to antibody harvesting and purification to final formulation molding, the bioreactor and tangential flow filtration system together guarantee the high efficiency, stability and controllable quality of antibody drug production, which promotes the development and application of antibody-drug couplings and monoclonal antibody drugs, and makes an important contribution to the cause of human health.
Here is the Holves brand website, https://www.bjholves.com/. Providing different types of industry information, technical knowledge, and solutions, we have developed and produced several new laboratory fermenter, bioreactor, tangential flow filtration system and other equipment to meet your needs from experimental to industrial production.
-
Bioreactor
Precise environmental control
1. Temperature control
During the culture process, the right temperature (37°C) is essential to maintain normal cell metabolism and growth rate. Similarly, during the antibody production phase, small fluctuations in temperature can affect the activity of intracellular enzymes, which in turn can alter cellular metabolic pathways and the rate of antibody synthesis. For the antibody component of ADC drugs, a stable temperature helps to ensure proper post-translational modification processes such as folding and glycosylation, which have stringent temperature requirements. The right temperature improves the quality and activity of the antibody, and provides high-quality antibody raw material for subsequent coupling to the drug linker.
HOLVES bioreactors use electric heating, coil heat transfer (jacketed temperature control is also available), combined with sophisticated temperature sensors and controllers, to precisely control the temperature inside the tank to the temperature required for cell growth.
2. pH adjustment
Cells produce acidic or alkaline substances, such as lactic acid and ammonia, during growth and metabolism. Depending on the needs of the cell line, the bioreactor has to maintain the pH value of the culture medium in a range suitable for the growth of the cells (generally 7.2 - 7.4). In the coupling reaction stage of ADC drug preparation, pH value affects the binding efficiency and selectivity of the drug linker to the antibody, and an inappropriate pH value may lead to heterogeneous coupling, resulting in a poor quality ADC drug product.
Changes in the value are closely monitored by a pH monitoring system and adjusted by the addition of an acid or base solution through an automated control system. Optionally, control can be performed using CO₂ and acid or base solution addition.
3.DO (Dissolved Oxygen) Concentration Management
Adequate oxygen supply is essential for cell growth and antibody production. The bioreactor automatically controls the DO concentration in the fermenter by adjusting parameters such as aeration, stirring speed and oxygen concentration to meet the oxygen demand of the cells. The appropriate level of dissolved oxygen can affect the metabolic state of the cells, which in turn affects the glycosylation level of the antibodies and has an important impact on the activity, stability and in vivo pharmacokinetic properties of the ADC drug.
4. Cell growth process to monitor
Viable Cell Density: During the whole cultivation process, a small amount of samples need to be taken out of the bioreactor periodically to monitor the growth status of the cells, and to judge whether to adjust the cultivation conditions according to the growth situation, in order to ensure that the cells are in the optimal state of growth and production. You can also choose to assemble a real-time detection of live cell density sensor to save labor and time as well as improve productivity.
Anti-foaming system: During the cell culture process, foam may be generated due to operations such as aeration and agitation. HOLVES fermenters are equipped with defoaming devices such as mechanical defoaming paddles or automatic addition of defoamer.
The configuration of sensors for ORP, online OD, and tail gas analysis (including OUR, CER, RQ, etc.) allows the cell growth status to be monitored at all times.
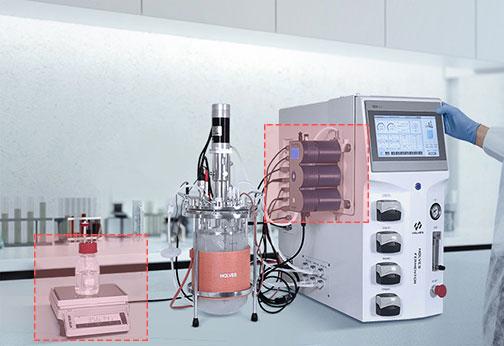
-
Tangential Flow Filtering System (TFF)
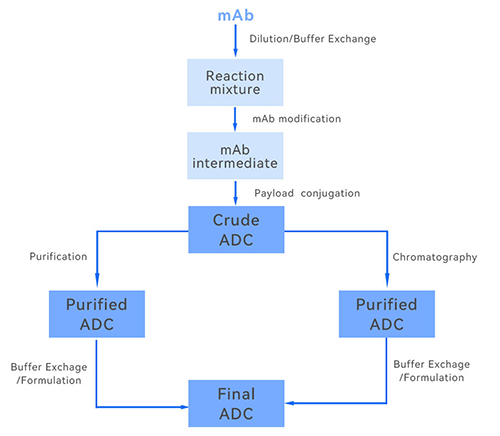
In the production of antibody drugs, the concentration of antibodies is often low, and they need to be concentrated to increase their concentration to meet the needs of subsequent processes and quality control. The tangential flow filtration system can effectively retain antibody macromolecules by selecting membranes with appropriate pore sizes, allowing small molecule impurities and water to pass through the membrane, thus realizing the concentration of antibodies. Meanwhile, during the concentration process, the salts and buffer components in the antibody solution can also be removed to achieve the effect of desalination, providing pure antibody raw materials for the subsequent coupling reaction or other process steps.
2. Purification of products
For ADC production, after coupling reaction, tangential flow filtration system can further play its purification role. By selecting filter membranes with different pore sizes, TFF technology can remove unreacted antibodies and small molecules of drugs and realize the separation of ADC from free toxins or antibodies. This process is important for improving the purity and quality of ADC products, ensuring the structural integrity and pharmacodynamic properties of the final drug product.
3. Buffer exchange
Tangential Flow Filtration systems can also be used to replace the buffer in a drug formulation. Through TFF technology, the original buffer in the drug solution is exchanged for a liquid that is more conducive to achieving storage stability, thus ensuring the stability and activity of the drug.
-
Synergy: Creating an Efficient Antibody Drug Production Chain
Meanwhile, the tangential flow filtration system is not only capable of efficiently concentrating and purifying the antibody during the downstream processing to improve the purity and quality of the antibody, but also capable of replacing the buffer to optimize the stability and activity of the drug preparation. This process lays a solid foundation for the final molding of the antibody drug, ensuring the performance and safety of the drug product.
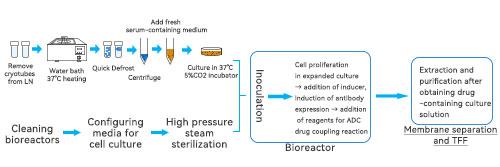
Through the synergistic effect of the two, from cell culture to antibody harvesting and purification to final formulation molding, the bioreactor and tangential flow filtration system together guarantee the high efficiency, stability and controllable quality of antibody drug production, which promotes the development and application of antibody-drug couplings and monoclonal antibody drugs, and makes an important contribution to the cause of human health.
Here is the Holves brand website, https://www.bjholves.com/. Providing different types of industry information, technical knowledge, and solutions, we have developed and produced several new laboratory fermenter, bioreactor, tangential flow filtration system and other equipment to meet your needs from experimental to industrial production.