In the field of modern bioengineering, the production of microbial enzymes has become a highly dynamic and potential industry. Enzymes, as an efficient biological catalyst, are widely used in many industries such as food, medicine and chemical industry. In recent years, ceramic membrane technology has gradually become a key process in enzyme production. This precision separation system constructed with inorganic materials is reshaping the purification pattern of enzyme production, and has demonstrated excellent performance and a wide range of application prospects in practical applications.
Precision separation
The porous structure of the ceramic membrane is like a molecular scale sieve, and its pore size distribution can be precisely controlled at the nanometer level. This feature enables precise sieving at the molecular level, effectively separating the target enzyme molecules from impurities in the fermentation broth. In the production of industrial grade proteases, ceramic membranes are used for clarification and concentration of the fermentation broth. By selecting the appropriate pore size ( usually 50-100 kDa), ceramic membranes are able to effectively retain the target protease enzyme while removing bacteria, cellular debris and other macromolecular impurities. This process not only improves the purity of the enzyme, but also significantly reduces the burden of subsequent purification steps.
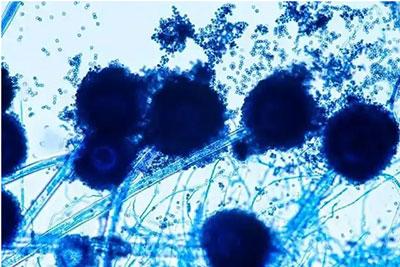
Stable operation
Ceramic membranes are resistant to high temperatures, acids and alkalis in industrialized production, enabling them to adapt to a variety of extreme operating conditions. For example, in the process of Bacillus subtilis fermentation production of amylase, ceramic membranes can operate stably under the harsh conditions of 80 ℃, pH 10, and run continuously for hundreds of hours without performance degradation, maintaining a stable flux of more than 100 LMH, with a retention rate of up to 99%. This stability significantly improves production efficiency and product quality, and also reduces the frequency of equipment maintenance and replacement, thus lowering production costs.
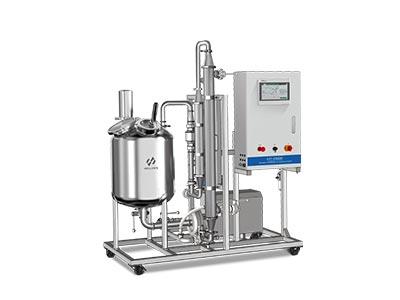
The surface properties of ceramic membranes are carefully designed to achieve selective separation of specific enzyme molecules by physical adsorption or chemical bonding. In practical applications, the recovery of target enzymes can be significantly improved by modulating the zeta potential and hydrophilicity of the membrane surface. For example, in lipase purification process, the surface modified ceramic membrane can increase the recovery of enzyme activity to over 95%, while controlling the removal of heteroprotein to over 90%.
Ceramic membrane filter technology is driving the transition of microbial enzyme production to green manufacturing. Its closed operating system can effectively reduce the use of organic solvents and reduce environmental pollution. At the same time, the high separation efficiency of ceramic membranes significantly reduces water consumption by more than 30% compared to traditional processes. Driven by the concept of sustainable development, this green manufacturing model is gaining wide recognition worldwide.
In all, the practical application of ceramic membrane technology in the production of microbial enzymes not only enhances the purity and quality of the product, but also promotes the greening and intelligentization of the production process. With the continuous progress of technology, ceramic membrane will continue to play its unique advantages in the field of biomanufacturing, and bring more innovations and breakthroughs for enzyme production.
Here is the Holves brand website, https://www.bjholves.com/. Providing different types of industry information, technical knowledge, and solutions, we have developed and produced several new laboratory fermenter, bioreactor, tangential flow filtration system and other equipment to meet your needs from experimental to industrial production.
Ceramic membrane filter technology is driving the transition of microbial enzyme production to green manufacturing. Its closed operating system can effectively reduce the use of organic solvents and reduce environmental pollution. At the same time, the high separation efficiency of ceramic membranes significantly reduces water consumption by more than 30% compared to traditional processes. Driven by the concept of sustainable development, this green manufacturing model is gaining wide recognition worldwide.
In all, the practical application of ceramic membrane technology in the production of microbial enzymes not only enhances the purity and quality of the product, but also promotes the greening and intelligentization of the production process. With the continuous progress of technology, ceramic membrane will continue to play its unique advantages in the field of biomanufacturing, and bring more innovations and breakthroughs for enzyme production.
Here is the Holves brand website, https://www.bjholves.com/. Providing different types of industry information, technical knowledge, and solutions, we have developed and produced several new laboratory fermenter, bioreactor, tangential flow filtration system and other equipment to meet your needs from experimental to industrial production.