-
Characteristics of E. coli and fermentation environment requirements
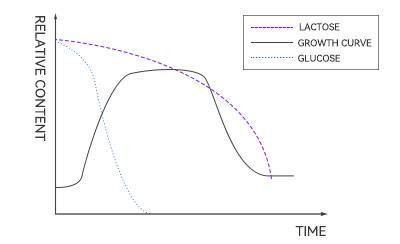
-
Importance of temperature control in E. coli fermentation
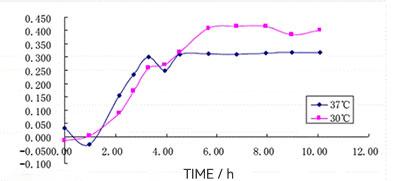
Phased temperature regulation can significantly optimize bacterial growth and product synthesis. For example, during the induction phase, appropriately increasing the temperature can enhance the expression of target proteins, while during the stabilization phase, decreasing the temperature helps to reduce the accumulation of by-products. This characteristic was utilized for the process staged temperature control strategy: at the early stage of induction (13.5-20h), 40°C was used for induction temperature; from 21 to 37h, the temperature was lowered to 38°C; after 38h, 36°C was used, and the final yield of synthesized L-Phe by the engineered bacteria reached 52.7 g/L, which significantly improved the growth of the organisms and the production of L-Phe [2].
HOLVES fermenter supports flexible setting of temperature parameters for different time periods according to the needs of different users' fermentation processes, realizing full automatic control. The specific operation interface is shown in Figure 1 below. In addition to temperature, dissolved oxygen, pH, stirring speed and refill pump speed can also be set, which not only saves a lot of labor and time costs, but also significantly improves the stability and efficiency of the fermentation process.
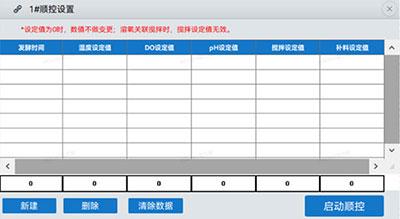
-
Effect of dissolved oxygen and pH on the growth of E.coli
In addition to temperature control, dissolved oxygen and pH are two other key factors affecting E. coli fermentation. The growth and metabolic activities of E. coli are highly dependent on the supply of oxygen, and insufficient dissolved oxygen will lead to the obstruction of the bacteria's metabolism, which in turn will affect the product synthesis. The level of dissolved oxygen depends on the amount of ventilation, stirring speed, the diameter-to-height ratio of the fermenter, the size of the stirring blade diameter, as well as the concentration of the culture solution, the incubation temperature, the vessel pressure and other factors [3].
HOLVES fermenters are designed to ensure that the dissolved oxygen concentration in the fermentation broth is maintained at a suitable level by optimizing the vessel's diameter-to-height ratio and by configuring paddles of the appropriate size and type, while the HF-Control control software correlates the dissolved oxygen value with the stirring rate and aeration volume, automatically adjusting them within the range.
Meanwhile, the strict control of pH value is also the key to the success of E. coli fermentation. For example, when exploring the effect of different pH values on the fermentation of isoleucine in E. coli, it was found that the control of the fermentation solution pH to keep 7.2 in the early stage can shorten the pre-bacterial delay period, the mid-term pH 7. 0 can reduce the maximum specific growth rate and reduce the generation of acetic acid, and the late stage pH 6.7 can effectively reduce the concentration of NH4 + and slow down the decline of the bacteria, so that the bacterial biomass and the production of isoleucine can be effectively improved. [4]
High or low pH will directly affect the growth of the bacteria and the accumulation of metabolites. The automated control system of the HOLVES fermenter can monitor the pH value in real time and maintain the acid-base balance of the fermentation broth through the operation of acid or alkali replenishment.
By precisely controlling the dissolved oxygen and pH, the HOLVES fermenter not only optimizes the growth environment of E. coli, but also improves the fermentation efficiency and product quality.
-
Compatibility and batch stability of fermenters for high-density culture of Escherichia coli bacteria
It has been shown that high-density fermentation is influenced by a variety of factors, such as expression system, medium composition, control of fermentation conditions, and replenishment strategies. [6] In addition to the high-precision parameter control described above, HOLVES has developed a variety of dosing methods for different fermentation scenarios. The most basic ones are constant speed manual replenishment and periodic on-time replenishment, as well as equation and exponential replenishment which are more suitable for high-density fermentation, as shown in Figure 2 below. The replenishment rate is in an equation or exponential relationship with the growth rate of the bacteria, which maintains nutrient concentrations and reduces the accumulation of metabolic by-products. In the study of human growth hormone production by recombinant E. coli, the exponential flow plus replenishment strategy was used, and the bacterial concentration reached 120 OD525.[7]

Batch stability in E. coli fermentation is also one of the key issues in industrial production. holves fermenters are designed to optimize the design and precise control of parameters, but also to ensure that all hardware parameters on the tanks are rigorously calibrated to minimize inter-unit variability. Multiple fermenter systems (e.g. Twin220 and Hub240) support parallel fermentation with synchronized control and real-time monitoring of key parameters (e.g. temperature, pH, dissolved oxygen, stirring speed, aeration, etc.) in parallel fermenters to ensure consistency and reproducibility of the fermentation process across batches.
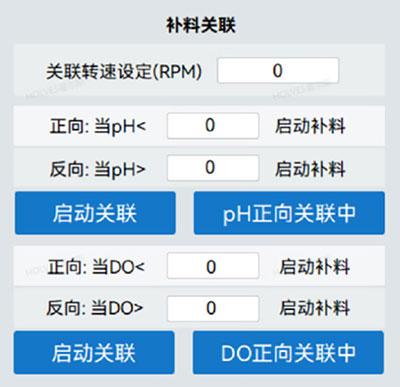
References:
[1] Du L H, Yuan J Y, Zhan J J, et al. Optimization of fermentation process for L-tyrosine production by Escherichia coli [J]. Food and Fermentation Science & Technology, 2024, 60(05): 16-22.
[2] Zhou H Y, Liu L, Du G C, et al. Effects of induction temperature on L-phenylalanine production by Escherichia coli BR-42 ΔpykA(pAP-B03) [J]. Food and Fermentation Industries, 2014, 40(04): 7-12. DOI: 10.13995/j.cnki.11-1802/ts.2014.04.014.
[3] Factors affecting the level of dissolved oxygen in culture media? [J]. Fermentation Science and Technology Bulletin, 2009, 38(04): 30.
[4] Sun J K, Wu X J, Shi J M, et al. Effect of pH on isoleucine fermentation by Escherichia coli [J]. Food and Fermentation Industries, 2012, 38(03): 12-16. DOI: 10.13995/j.cnki.11-1802/ts.2012.03.012.
[5] Li H P, Huang H C, Zhong W H. Advances in high-density cultivation of Escherichia coli [J]. Chemistry and Bioengineering, 2012, 29(08): 1-5.
[6] Ji C F, Liu Z, Ma L N, et al. Progress in high-density and high-expression cultivation of recombinant Escherichia coli [J]. Biotechnology, 2022, 32(02): 246-251. DOI: 10.16519/j.cnki.1004-311x.2022.02.0040.
[7] Li M, Chen C Q. Advances in high-density fermentation of recombinant Escherichia coli [J]. Progress in Biotechnology, 2000, 20(02): [No pagination provided].
[8] Meng J Z, Chen F Z, Wang Q Y, et al. pH-stat high-density fermentation of recombinant trehalose synthase engineered strain [J]. Science and Technology of Food Industry, 2006, (08): 125-128.
[9] Li Y, Pu Q, Zhao Z L, et al. Dissolved oxygen feedback-fed-batch high-density cultivation of engineered E. coli for human bone morphogenetic protein-2 production [J]. Chinese Journal of Biotechnology, 2002, (06): 718-723. DOI: 10.13345/j.cjb.2002.06.016.
Here is the Holves brand website, https://www.bjholves.com/. Providing different types of industry information, technical knowledge, and solutions, we have developed and produced several new laboratory fermenter, bioreactor, tangential flow filtration system and other equipment to meet your needs from experimental to industrial production.